case
事例インタビュー
キリンビール株式会社様
キリンビールが実現した
FlaRevo※による製造現場の革新!
※製造業向けビデオマネジメントシステム
製造現場のデジタル化が進む中、キリンビール株式会社(以下キリンビール)は2019年、「FlaRevo」の導入を決断しました。従来の「監視カメラ」の枠を超え、直感的な操作性と高い拡張性を備えたこのシステムは、キリンの工場に大きな変革をもたらしています。品質管理や安全管理はもちろん、技術伝承まで、その活用領域は広がっています。
現在では関連会社も含めて4,000台以上のカメラが稼働し、製造現場の「目」として欠かせない存在となったFlaRevo。この記事では、キリンビールの先進的な取り組みを通じて、映像活用が切り拓く製造現場の未来を探ります。
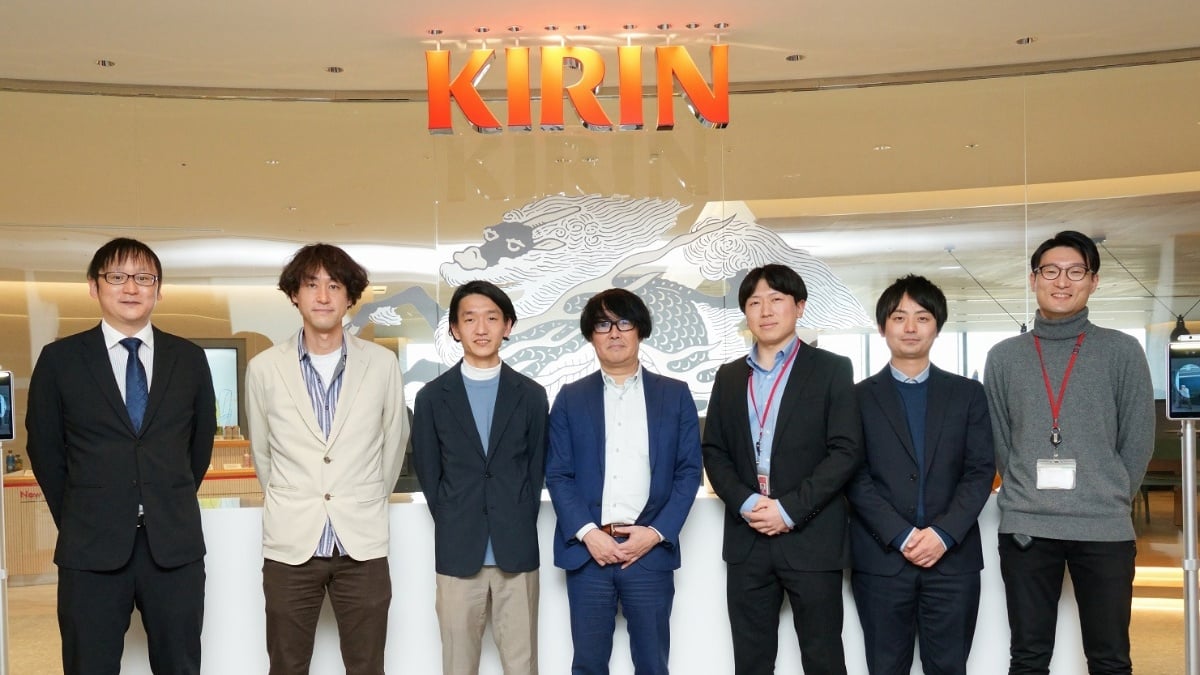
キリンビールの挑戦
製造現場の"目"として進化するカメラシステム
FlaRevo導入の経緯について、技術部(当時)でカメラシステム導入の構想から選定、立上げを主に担った齊川匡氏、取手工場でカメラの現場導入・定着に取り組み、現在は技術部で全国の工場への展開を進める宮浦直人氏、そして取手工場で新機能の開発と社内展開を推進する立場の溝井航平氏の3名にお話を伺いました。
INTERVIEWEE

今回お話を伺ったキリンビールのメンバー
左から:
取手工場パッケージング担当 溝井 航平 氏
企画部 齊川 匡 氏
技術部 宮浦 直人 氏
※インタビュー当時所属
製造現場の課題解決の糸口に
「探偵のような作業」からの解放
導入の背景には、製造現場の課題がありました。「工場のラインは生き物のようなもので、様々なトラブルが発生します。そのトラブルが、品質に影響があるのかどうかを評価しなければなりません」と齊川氏は説明します。
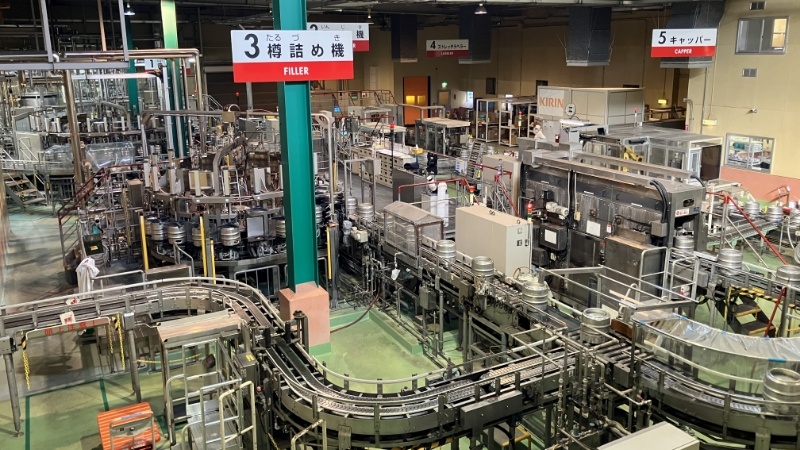
例えば、缶がへこんでいるのを発見した場合には、それがいつ、どこで、どのように発生したのか、原因を特定して対応する必要があります。「カメラが導入される前は、『このキズはいつ、どこでどうやってついたのだろう……』と、まるで探偵のような作業をしていました」と齊川氏。「この辺りで受けてこうなったのではないか」と推測しながら対策を講じても、また同じような問題が発生する。原因は別の所にあったのではないか……。そんな試行錯誤の日々が続いていたといいます。
また「コンベアで今、缶がどこまで流れてきたか」というような現場の情報についても、以前はその場所まで確認に出向く必要がありました。このようなちょっとしたことも含め、「現場で働く人の業務負荷を削減するためにも、品質面でも、トラブル対応の面からも、カメラシステムが必要」と考え、齊川氏はカメラシステムの導入検討を始めました。
決め手となった4つの強み
徹底検証で選び抜かれたFlaRevo
導入検討にあたり、齊川氏は選択肢となったカメラシステムを一通り入手して、徹底的な比較検討を行いました。その結果、株式会社RYODENが提案したFlaRevoが採用されることとなりました。決め手となったのは、主に次の4点でした。
1. 直感的なユーザーインターフェイス
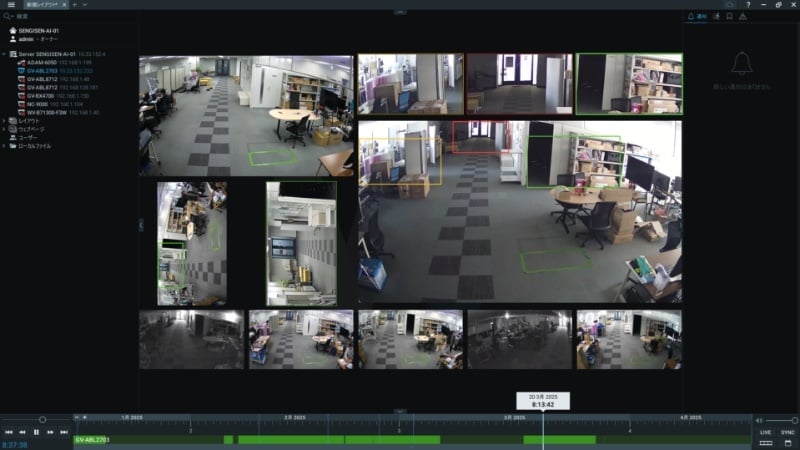
「他のシステムと比べて、ユーザーインターフェイスが圧倒的に優れていました。いろいろな操作が直感的でとにかく早いという点が大きかったと思います」
(齊川氏、以下同)
2. 柔軟な拡張性
「比較対象のカメラシステムは、特定メーカーのカメラしか接続できないシステムが多かったのですが、FlaRevoは約400のメーカー、6,000以上の機種に対応しています」
3. 継続的な機能追加
「iOSのように頻繁にバージョンアップされ、新機能が追加されていく点も魅力でした。一般的なVMSは一度導入したらそのままの形でずっと使っていくシステムが多いと思いますが、FlaRevoはどんどん新しい機能が追加されていきます」
4. コスト面での優位性
「カメラを見るシステムの部分(Nx Witness)については、ライセンスに更新費が発生しない「買い切り」の形式でした。FlaRevoの追加機能や保守・メンテナンスについては別途契約していますが、基本ソフトの利用については1度買えばランニングコストがかからないと点も大きな決め手になりました」
抵抗感から歓迎へ
現場の意識を変えた戦略的導入アプローチ
システムの選定後、次の課題となったのが現場への導入です。「現場担当者のITリテラシーの課題もありましたが、"監視されている"という不安の声もありました」と宮浦氏は説明します。これら現場導入の課題については、齊川氏による2つの粘り強い導入活動で乗り越えていきました。
1つ目は、無線式の試験用キットの製作です。
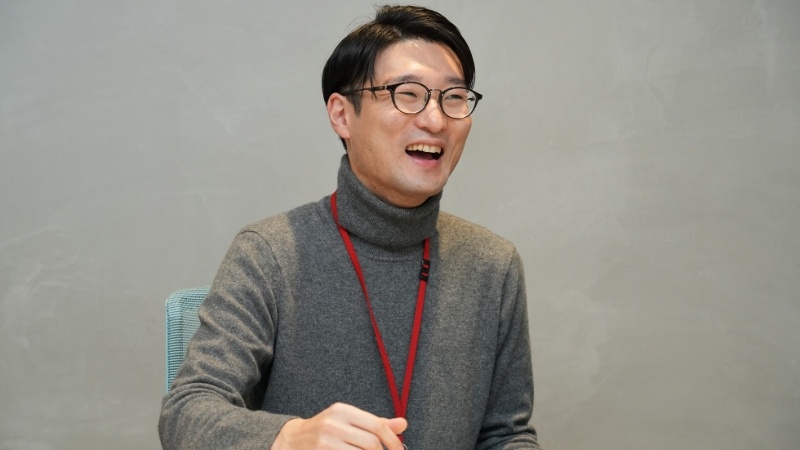
現場テスト用の無線キットを自作し、さらに100ページに及ぶマニュアルを作成した齊川氏
カメラの映像は安定性の面から最終的には有線接続が必要ですが、最初から配線工事をしてしまうと位置の変更が難しくなります。そこで、まずは無線で試せる環境を整え、効果的な設置場所を見極めてから配線を含めて本設置する、という手順で導入を進めていきました。
齊川氏はこのキットを1個自作し、以後は業者の力も借りて、9工場に各10個、全90個を配布しました。
2つめは、100ページに及ぶ設定・操作マニュアルです。齊川氏は、現場の作業者も見ればわかるように「IPアドレス」や「ネットワーク」など、基本的なことから説明するマニュアルを作りあげました。そのうえで、工場ごとに説明会を実施し、現在では現場スタッフが自らカメラを使いこなすようになりました。
システム導入のもう一つの大きな課題が、セキュリティの確保でした。「社内のセキュリティ部門は標準外のシステムに対して非常に慎重です。特に、製造ラインの映像は重要な機密情報ですから、映像の流出リスクなどについて厳しい指摘を受けました」と齊川氏は説明します。セキュリティ部門との折衝には時間がかかりましたが、システムの安全性を一つ一つ丁寧に説明し、RYODENの協力も得て必要な対策を講じることで理解を得ていきました。
トライアルの成果を全国の工場へ
成功体験の水平展開
このような地道な取り組みが実を結び、次第に現場からも「ここにもカメラがあると便利」という声が上がるようになっていきました。
「最初は缶製品ラインだけでスタートしました」と宮浦氏は説明します。
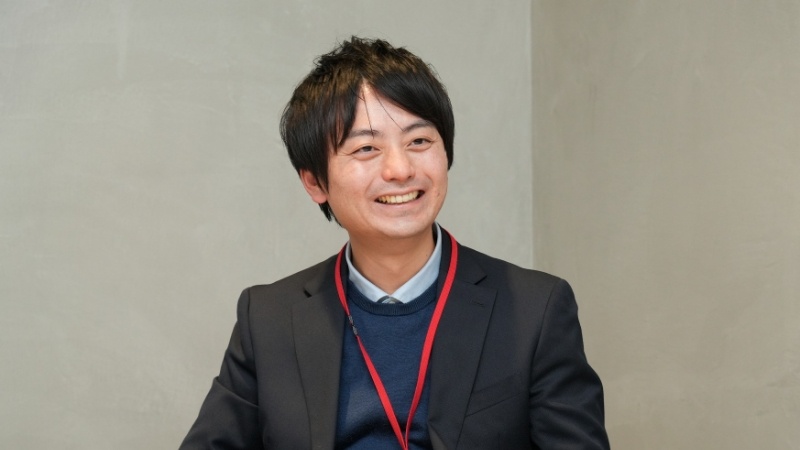
カメラシステムの全国9工場への展開を支えた宮浦氏
そこで効果的なカメラの配置場所や運用方法を確立し、他ラインへ展開をしていきました。
その後、壜製品や樽製品のラインへと展開を拡がっていきます。「各工場から担当者を集めてプロジェクトチームを作り、壜ライン、樽ラインなど、それぞれの場所で効果的な活用方法の検討も実施しました」と宮浦氏。「例えば壜ラインならここにカメラを置くと便利、という具体的な設置場所まで含めたベストプラクティス集を作成し、それを基に展開を進めました」
このように、一つのラインで実証された効果を基に、他ラインへと展開していく手法が功を奏し、現在ではキリンビールの9工場に加え、キリンビバレッジや協和発酵バイオなどグループ会社にもカメラシステム導入が広がっています。グループ全体では4,000台を超えるFlaRevoのカメラが稼働し、製造現場の「目」として稼働するようになりました。
年間1,000時間以上の工数削減を実現
数字で見る業務革新
FlaRevo導入による業務効率化の効果は、具体的な数字にも表れています。主な改善事例を見ていきましょう。
1. 排水処理場での点検業務
ビール製造では、製造工程で出る排水を微生物処理して浄化する必要があります。これまで処理槽の状態は担当者が現場まで足を運んで目視確認していました。これが監視室からカメラの確認で済むようになりました。
-
改善:遠隔監視で確認可能に
-
効果:年間365時間の工数削減
2. 製造ラインでの製品切り替え状況確認
例えば缶ビールの製造ラインで、350mlから500mlへなど製品サイズを切り替える際に、ライン上に前の製品が残っていないことを目視確認にて行っていました。これをカメラに切り替えて、目視確認の工数と時間を削減しました。
-
改善:カメラによる遠隔確認が可能に
-
効果:1工場あたり年間約800時間の工数削減
3. トラブル発生時の品質確認
製造ラインで何らかの異常が見つかった場合、その影響を受けた可能性のある製品をすべて確認する必要があります。例えば30分前の点検で異常がなく、次の点検で問題が見つかった場合、その間に製造された製品を全て確認する作業に膨大な人手と時間がかかっていました。これをカメラに切り替えたことで、トラブルの時間と場所をピンポイントで特定でき、それが品質に影響するかどうかもすぐに判断できるようになりました。
-
改善:映像から問題発生時点を特定し、確認範囲を最小化
-
効果:確認作業の大幅な効率化と、品質管理の確実性向上
「普段は、1工場あたり年間800〜1,000時間の工数削減効果が出ています、と説明しています。でも実際には、もっと削減効果が出ていると思っています」と宮浦氏は話してくれました。「最初は映像を撮られることに抵抗もありましたが、今は現場から『カメラがあって良かった』という声が上がるようになりました」(溝井氏)
映像共有がもたらした情報伝達の変革
FlaRevo CLIP
現在、現場で活用が進んでいるのが、映像の一部をブックマークする「FlaRevo CLIP」という新機能です。発案者の齊川氏は「録画した映像資産が3ヶ月程度で上書きされてしまうのはもったいない」と考え「重要な部分だけを取り出して保存・共有できる仕組みを」という要望をRYODENに伝えました。
その要望に応えて開発された新機能「FlaRevo CLIP」について、齊川氏から開発を引き継いだ溝井氏に伺いました。
1.直感的な操作性
製造現場でトラブルなどが発生したタイミングの映像を一部だけ切り取って、ワンクリックでCLIPに登録して保存。特別な知識や複雑な操作は必要なく、現場のスタッフもすぐに使えるようになりました。
2.ブラウザベースの共有機能
動画共有サイトのような専用のWebサイトで共有できるため、関係者が必要な時に確認できます。従来のようにメモやUSBメモリを使って、何度も説明のやり取りをする必要もなくなりました。
3.コメント機能による情報共有
映像に対してコメントを付けられ、対策の検討や情報共有に活用できます。文章だけでは伝わりにくい細かな状況も、映像があることで正確に共有できるようになりました。
取手工場への導入から約1年が経過し、CLIP機能は現場に定着しつつあります。「現場からは"CLIPしておきました"という報告が日常的に上がってくるようになり、朝会での報告や部署間の情報共有が格段にスムーズになりました」と溝井氏は手応えを語ります。
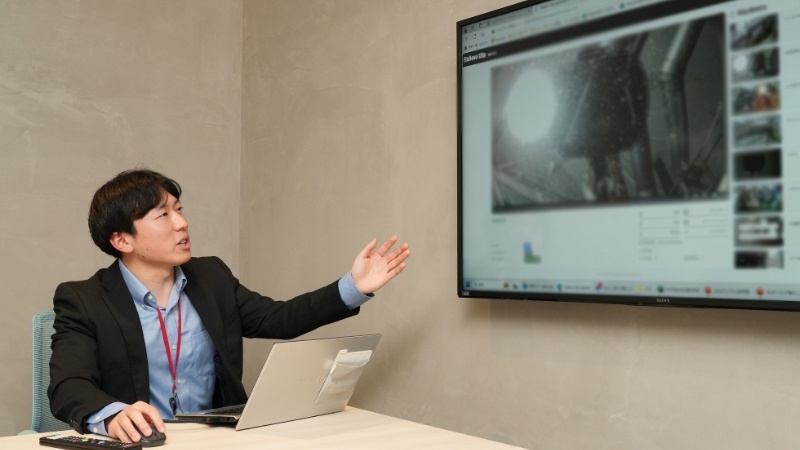
CLIP機能の現場活用について説明する溝井氏
例えば夜勤の時間帯に起きた事象を朝会で共有する際、以前は文章での報告だけでしたが、今はCLIPした映像を見ながら具体的な議論ができます。映像があることで、言葉では伝えにくい微妙な違いや、ちょっとした気付きを共有できるようになりました。
取手工場での活用成果を受けて、CLIP機能は今後、全工場への展開が決まったということです。
データ活用で広がる次世代工場管理
AI×FlaRevoの可能性
キリンビールが最近力を入れている映像活用の取り組みのひとつに、AIを活用した機能拡張があります。現在進行中の主なプロジェクトを見ていきましょう。
1. 工場作業の安全確認の強化
会社の最重要課題である安全について、カメラの画像解析をAIで行う取り組みを、滋賀工場で先行検証しています。ヘルメットや保護具の着用をAIで確認して着用していない人がいたらアラームを出す、立ち入り禁止エリアに人が入るとインターロックが作動するなどの機能は既に稼働が始まっており、2025年6月の評価完了を目指し、滋賀工場でのトライアルが進行中です。
2. カートンの破れ検知機能
AIを活用したカートンの破れ検知機能については、キリンビールの要望を受け、RYODENでの機能開発が進んでいます。現在は定期的な抜き取り検査を行っていますが、カートンの破れをAIで自動検知できれば、現在行っている抜き取り検査やビデオを見直す確認作業などを省略できる見込みです。「カートンには柄もありますので、キズか柄かの判別など難しい部分もありますが、今後実現したいテーマのひとつになっています」(宮浦氏)
3. パレット点検の自動化
工場に返却される物流用パレットについて、現在は洗浄/再利用/廃棄の判断を人手をかけて行っています。「この作業を自動化できないか、という我々からの要望に対し、RYODENさんからAIを活用した検査システムを提案いただいています」と宮浦氏は説明します。こちらは確度の高い判定を行うため、FlaRevoカメラシステムの枠を超えた画像検査システムとして開発が進んでおり、早期の実用化を目指しています。実現すれば1工場あたり年間1,000万円のコスト削減が見込めるということです。
広がるFlaRevoの活用領域
技術伝承から予知保全まで
FlaRevoの活用範囲は、日々の業務改善から将来を見据えた取り組みまで広がっています。例えばCLIP機能を活用して動画マニュアルの作成が始まっており、将来の若手育成に向けたコンテンツ作りが進められています。予知保全や作業環境の改善に向けた取り組みについては、映像分析で得られた知見を基に、作業者の負担を減らしてより良い現場環境づくりを目指すプロジェクトが進行中です。また、PLC連携機能「FlaRevo CONNECT」についても、今後活用を進めていきたいということです。
運用開始からまだ1年で様々な活用の可能性が見えている現状について、溝井氏は「これが5年、10年経ったときに、この映像が大きな資産になっていると思います」と期待を込めます。
FUTURE
映像データが創る製造現場の未来
導入開始5年が経ち、FlaRevoのカメラシステムは、キリンビールの工場に変革をもたらし続けています。当初は「監視されている」という抵抗感もあった現場スタッフからも、今では「CLIPしておきました」という報告が自然に上がってくるようになり、現在FlaRevoは現場に欠かせないツールとして定着しました。
映像を活用した業務改善は、品質管理や安全管理にとどまらず、技術伝承やノウハウの共有にまで広がっています。さらにAIとの連携による新機能の開発も進み、製造現場のデジタル化は着実に前進しています。キリンビールの取り組みはその先進的な事例であり、今後さらに多くの製造業へと広がりを見せていくことでしょう。
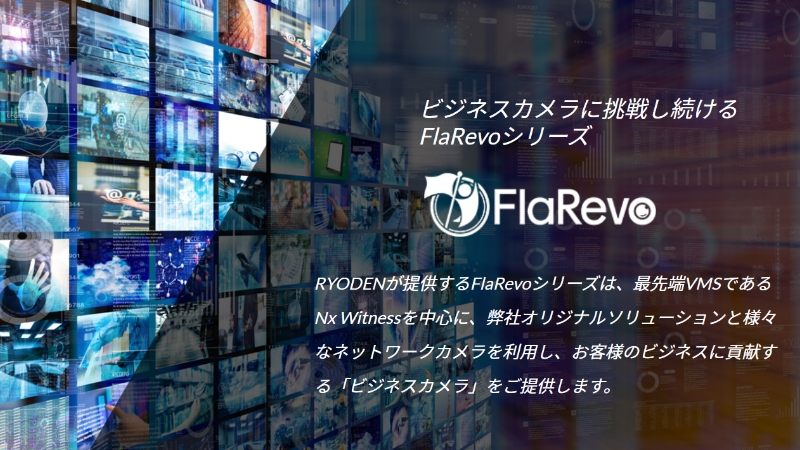